It would be logical to start this article with some myth debunking. The smart factory conception doesn't imply that one can deploy a certain software and revamp the whole manufacturing process overnight. Instead, the concept of intelligent manufacturing means using machine learning, artificial intelligence (AI), robotics, the Internet of Things (IoT), additive manufacturing, and augmented reality technologies in conjunction.
What is a smart factory?
As of today, the three main cornerstones are shaping the innovative factory concept:
- The dominance of IoT solutions, sensors, and industrial robots;
- The intensive use of automation and data insights;
- Better regulatory compliance.
A smart factory takes root in Industry 4.0, a new chapter in the history of the Industrial Revolution. Companies such as Siemens AG, Robert Bosch GmbH, Emerson Electric Company, and Yokogawa Electric Corporation are already using smart factory strategies to improve business processes based on real-time production data.
In regard to the changing industrial landscape, manufacturers are en masse digitizing their factories. Last year, the international smart factory market hit $270.74 billion in valuation. The market is forecasted to reach $461.82 billion by 2026, registering a CAGR of 9% during five years.
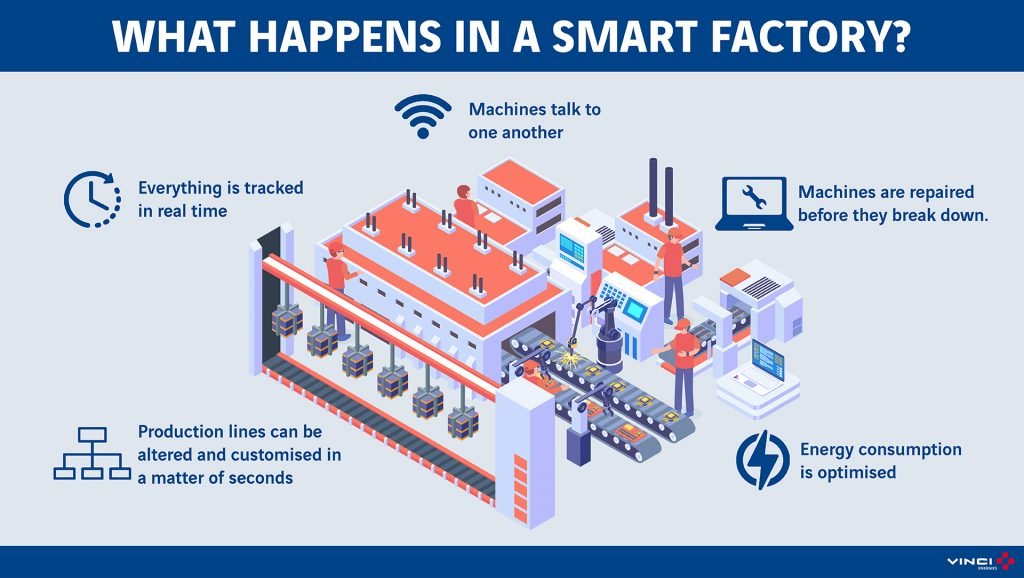
Suppose you leave aside all the marketing fluff that comes with intelligent factories in the media. In that case, the main thing about a smart factory is the transparency and interconnection of working processes and systems within an industrial plant. Industry 4.0 emphasizes the use of real-time data, sensors, automation, machine learning (ML), and technologies such as PLC, SCADA, MES, HMI, etc. Robots (including collaborative ones), additive technologies (3D and 4D printing), industrial avatars controlled via neural interfaces, and other solutions are widely used in smart factories as well. Let’s dive into details.
What is the impact of a smart factory on industrial businesses?
First, a smart factory allows production lines to operate mainly autonomously, with the possibility of self-correction. Such self-correction is the hallmark of Industry 4.0 and represents its significant advantage over traditional production. Self-optimization allows you to predict and identify quality deterioration dynamics more quickly and helps find specific causes associated with the human error factor, equipment, or the environment. This level of self-optimization is attributed to the fact that today's intelligent manufacturing systems can learn and adapt in real-time, making businesses far more agile than ever before.
Second, smart factories are all about higher efficiency and productivity. The modern factory's ability to predict future results based on previously acquired and real-time data can increase uptime and prevent security issues. You can say that this concept takes the best out of both industrial devices and employees. Third, smart factories help introduce agile production processes using data collection so that manufacturers can build their decisions based on uncovered insights.
From a purely business perspective, smart factories allow:
- lowering costs;
- reducing downtime;
- minimizing waste (a vital feature concerning today’s ecological regulations).
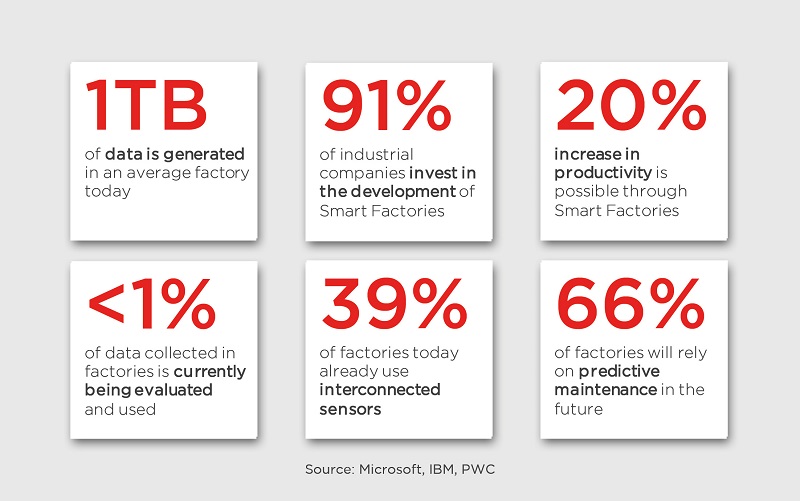
Companies that rely on smart factory technological and management solutions aim to obtain economic benefits already at the stage of producing small batches of products or even single copies. Traditionally, this effect was achieved by reducing costs associated with mass production. The flexibility of a smart factory is about the rapid restructuring of production from one product to another and ensuring the production of various products within a given time frame and at a given production cost.
Another significant benefit is the introduction of computer modeling technologies at the stage of product design. With the concept of digital twins, it is possible to predict equipment response to operational loads with 95% accuracy and reduce the operating costs of industrial complexes by up to 10%.
At the same time, it's worth saying that not just any enterprise will benefit from full automation and digitalization. The corresponding measures require significant capital costs, which in the case of small enterprises may never pay off. This way, you need to find a balance between automation and manual labor.
A smart factory concept can also provide tangible benefits for health and safety and environmental sustainability. The operational efficiency results in less environmental waste compared to conventional production processes and generally contributes to greater environmental sustainability. The higher degree of automation of production processes reduces the likelihood of human error in various situations, including industrial accidents.
Data, data everywhere
The industrial Internet has become the most popular element of a smart factory. The conception represents an integrated system for collecting, transferring, storing, and processing the production process data gathered from sensors that control machine tools, welding installations, melting furnaces, chemical reactors, etc. This data from sensors go to an IT system for further analysis. With revealed insights at hand, manufacturers can develop timely technological and management decisions.
The problem is most manufacturing businesses find themselves at the first level of smart factory maturation. That basically means that they have already successfully digitized and automated some working processes and operations. However, they don't take any actionable insights from the data they collect. In other words, collecting data doesn’t mean using it the proper way. The second and third maturity stages take data collection to a whole different level: dashboards and visualization tools make data accessible and understandable. This way, manufacturers can have a clear vision of what's going on inside their factories and make decisions proactively.
What's ironic is that, at the same time, the abundance of data is one of the main problems in smart factory expansion. Many companies haven't yet learned how to select relevant information on their technological processes. Instead, they accumulate all of it, which is non-efficient, to say the least. What's more, the sensors are often located in incorrect places, not reaching the system’s critical points and without understanding how the data is related to the technological process. The information's completeness is nowhere to be seen, which means that data is pretty much useless.
Challenges
Another serious challenge is of an economic (and somewhat human) nature. On the one hand, the transition to a smart factory comes with a tangible and beneficial economic impact. On the other hand, the whole process from A to Z is a lengthy and highly costly business. First, you have to restructure the entire production system and purchase expensive equipment for collecting, storing, and processing data. Second, it's necessary to create costly high-quality digital models (digital twins) of production.
And here’s where the problem lies. The management of a factory begins to consider the effect of digitalization and realizes that the possible savings it may bring will not be enough to recoup the costs of digitalization here and now. It might take several years to do so. What's the outcome? The purchase of expensive modern equipment seems a risky business, and many decision-makers refuse to carry on.
One more challenge is integrating new equipment with the current infrastructure and the compatibility of existing devices to the latest technology. The common situation is when the old equipment requires some protocols while new devices require some other. Machine-to-machine communication is all about a robust communication system. For instance, modern manufacturing systems need the IPv6 connectivity protocol to support several devices connected simultaneously.
Cybersecurity is vital too. As said earlier, smart manufacturing systems require reliable network connectivity. However, sharing information through the Internet is dangerous without proper end-to-end data encryption measures. To do so, manufacturers should protect all the network's nods against external interference and data mistreatment.
To Sum Up
Although the introduction of intelligent manufacturing technologies is associated with operational and financial risks, these risks can’t compete with the benefits that such technologies bring. In addition, most risks can be mitigated by implementing effective change management strategies, using measurable approaches to validating technology viability, and additional investment.
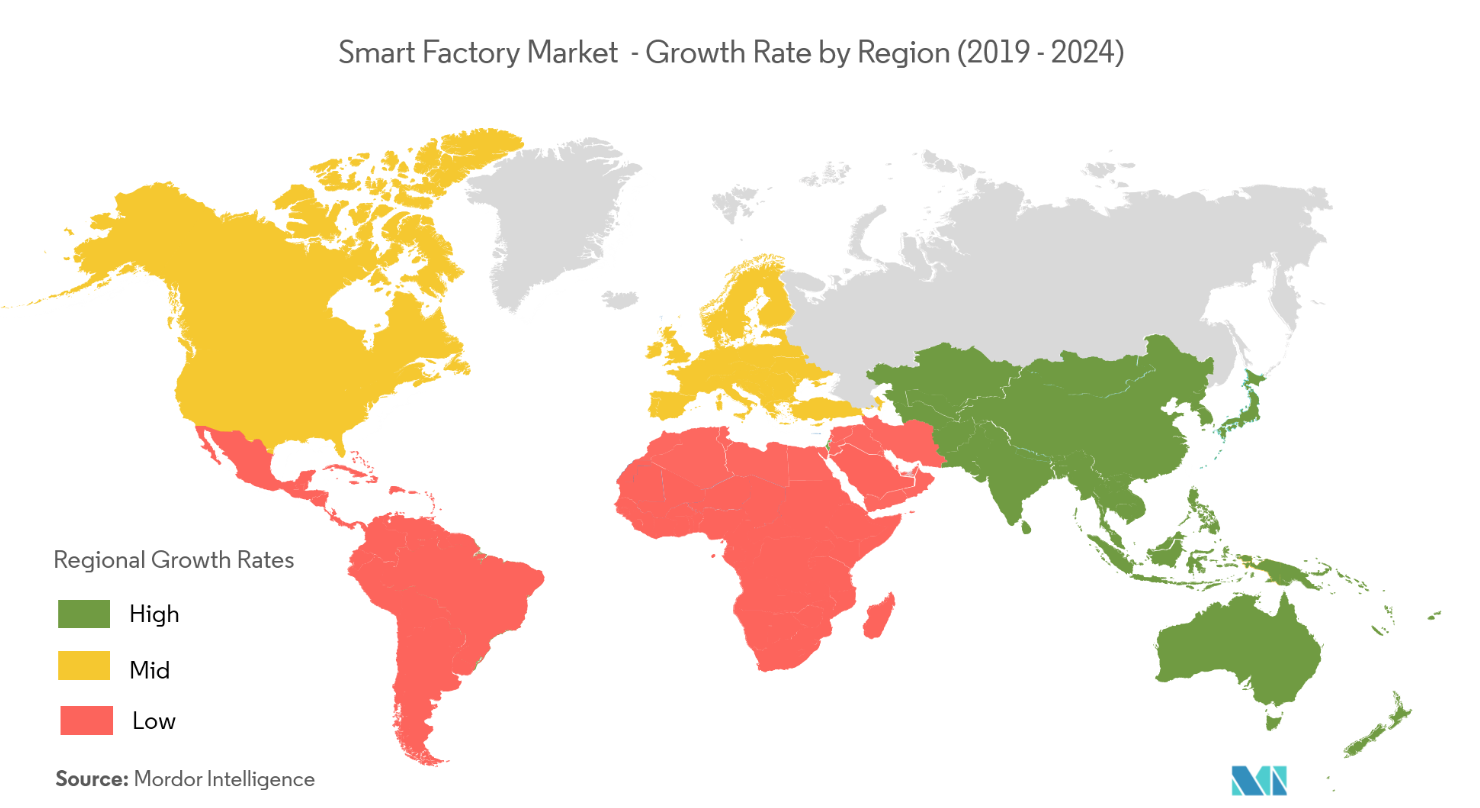
Despite the difficulties in the transition from traditional to smart production, there is no doubt that all modern players will have to change existing business models and adopt the concept of an intelligent factory. Every year, Industry 4.0 technologies will increasingly penetrate production processes and supply chains. The analysis of production's objective factors, equipment wear, and quality of raw materials make it possible to get the maximum return on equipment and ensure an increase in production volumes of up to 30%.
Do you think about making your factory smart? We invite you to transform your factory and reimagine production with Industry 4.0 technologies and Industrial Internet of Things (IIoT) consulting and development services. We build our client relations based on our long-standing experience in Industry 4.0 consulting and software development services. Contact us, and let’s start your journey towards digitalization today.
Streamlining Gifting Marketplace Operations with Retool
Afloat, a gifting marketplace, needed custom dashboards to streamline order management, delivery tracking, and reporting while integrating with Shopify and external APIs.
The solution:
We built two Retool-based dashboards:
- A Retail Partner Dashboard embedded into Shopify for managing orders and store performance.
- An Admin Dashboard for handling deliveries and partner data.
Both dashboards included real-time integration with Afloat's Backend and APIs for accurate, up-to-date data and scalability.
The result: enhanced efficiency, error-free real-time data, and scalable dashboards for high-order volumes.
Billing Automation for a SaaS Company with Low-Code
Our client needed a robust billing solution to manage hierarchical licenses, ensure compliance, and automate invoicing for streamlined operations.
The solution:
We developed a Retool-based application that supports multi-tiered licenses, automates invoicing workflows, and integrates seamlessly with CRM and accounting platforms to enhance financial data management.
The result:
- Achieved 100% adherence to licensing agreements, mitigating penalties.
- Automated invoicing and workflows reduced manual effort significantly.
- Dashboards and reports improved decision-making and operational visibility.
Retool Dashboards with HubSpot Integration
Our client needed a centralized tool to aggregate account and contact activity, improving visibility and decision-making for the sales team.
The solution
We built a Retool application integrated with HubSpot, QuickMail, and Clay.com. The app features dashboards for sorting, filtering, and detailed views of companies, contacts, and deals, along with real-time notifications and bidirectional data syncing.
The result
- MVP in 50 hours: Delivered a functional application in just 50 hours.
- Smarter decisions: Enabled data-driven insights for strategic planning.
- Streamlined operations: Reduced manual tasks with automation and real-time updates.
Lead Generation Tool to Reduce Manual Work
Our client, Afore Capital, a venture capital firm focused on pre-seed investments, aimed to automate their lead generation processes but struggled with existing out-of-the-box solutions. To tackle this challenge, they sought assistance from our team of Akveo Retool experts.
The scope of work
The client needed a tailored solution to log and track inbound deals effectively. They required an application that could facilitate the addition, viewing, and editing of company and founder information, ensuring data integrity and preventing duplicates. Additionally, Afore Capital aimed to integrate external tools like PhantomBuster and LinkedIn to streamline data collection.
The result
By developing a custom Retool application, we streamlined the lead generation process, significantly reducing manual data entry. The application enabled employees to manage inbound deals efficiently while automated workflows for email parsing, notifications, and dynamic reporting enhanced operational efficiency. This allowed Afore Capital's team to focus more on building relationships with potential founders rather than on administrative tasks.
Retool CMS Application for EdTech Startup
Our client, CutTime, a leading fine arts education management platform, needed a scalable CMS application to improve vendor product management and user experience.
The scope of work
We developed a Retool application that allows vendors to easily upload and manage product listings, handle inventory, and set shipping options. The challenge was to integrate the app with the client’s system, enabling smooth authentication and product management for program directors.
The result
Our solution streamlined product management, reducing manual work for vendors, and significantly improving operational efficiency.
Building Reconciliation Tool for e-commerce company
Our client was in need of streamlining and simplifying its monthly accounting reconciliation process – preferably automatically. But with a lack of time and low budget for a custom build, development of a comprehensive software wasn’t in the picture. After going through the case and customer’s needs, we decided to implement Retool. And that was the right choice.
The scope of work
Our team developed a custom reconciliation tool designed specifically for the needs of high-volume transaction environments. It automated the processes and provided a comprehensive dashboard for monitoring discrepancies and anomalies in real-time.
The implementation of Retool significantly reduced manual effort, as well as fostered a more efficient and time-saving reconciliation process.
Creating Retool Mobile App for a Wine Seller
A leading spirits and wine seller in Europe required the development of an internal mobile app for private client managers and administrators. The project was supposed to be done in 1,5 months. Considering urgency and the scope of work, our developers decided to use Retool for swift and effective development.
The scope of work
Our developers built a mobile application tailored to the needs of the company's sales force: with a comprehensive overview of client interactions, facilitated order processing, and enabled access to sales history and performance metrics. It was user-friendly, with real-time updates, seamlessly integrated with existing customer databases.
The result? Increase in productivity of the sales team and improved decision-making process. But most importantly, positive feedback from the customers themselves.
Developing PoC with Low Code for a Tour Operator
To efficiently gather, centralize, and manage data is a challenge for any tour operator. Our client was not an exception. The company was seeking to get an internal software that will source information from third-party APIs and automate the travel itinerary creation process. Preferably, cost- and user-friendly tool.
The scope of work
Our experts ensured the client that all the requirements could be covered by Retool. And just in 40 hours a new software was launched. The tool had a flexible and easy-to-use interface with user authentication and an access management system panel – all the company needed. At the end, Retool was considered the main tool to replace the existing system.
Testing New Generation of Lead Management Tool with Retool
Our client, a venture fund, had challenges with managing lead generation and client acquisition. As the company grew, it aimed to attract more clients and scale faster, as well as automate the processes to save time, improve efficiency and minimize human error. The idea was to craft an internal lead generation tool that will cover all the needs. We’ve agreed that Retool will be a perfect tool for this.
The scope of work
The project initially began as a proof of concept, but soon enough, with each new feature delivered, the company experienced increased engagement and value.
We developed a web tool that integrates seamlessly with Phantombuster for data extraction and LinkedIn for social outreach. Now, the company has a platform that elevates the efficiency of their lead generation activities and provides deep insights into potential client bases.
Building an Advanced Admin Portal for Streamlined Operations
Confronted with the need for more sophisticated internal tools, an owner of IP Licensing marketplace turned to Retool to utilize its administrative functions. The primary goal was to construct an advanced admin portal that could support complex, multi-layered processes efficiently.
The scope of work
Our client needed help with updating filters and tables for its internal platform. In just 30 hours we've been able to update and create about 6 pages. Following features were introduced: add complex filtering and search, delete records, styling application with custom CSS.
Together, we have increased performance on most heavy pages and fixed circular dependency issues.
Creating MVP Dashboard for Google Cloud Users
Facing the challenge of unoptimized cloud resource management, a technology firm working with Google Cloud users was looking for a solution to make its operations more efficient. The main idea of the project was to create an MVP for e-commerce shops to test some client hypotheses. Traditional cloud management tools fell short.
The scope of work
Determined to break through limitations, our team of developers turned Retool. We decided to craft an MVP Dashboard specifically for Google Cloud users. This wasn't just about bringing data into view; but about reshaping how teams interact with their cloud environment.
We designed a dashboard that turned complex cloud data into a clear, strategic asset thanks to comprehensive analytics, tailored metrics, and an intuitive interface, that Retool provides. As the results, an increase in operational efficiency, significant improvement in cost management and resource optimization.
Elevating CRM with Custom HubSpot Sales Dashboard
Our other client, a SaaS startup, that offers collaborative tools for design and engineering teams, was on a quest to supercharge their sales efforts. Traditional CRM systems were limited and not customizable enough. The company sought a solution that could tailor HubSpot to their workflow and analytics needs.
The scope of work
Charged with the task of going beyond standard CRM functions, our team turned to Retool. We wanted to redefine how sales teams interact with their CRM.
By integrating advanced analytics, custom metrics, and a user-friendly interface, our developers provided a solution that transformed data into a strategic asset.
In 40 hours, three informative dashboards were developed, containing the most sensitive data related to sales activities. These dashboards enable our customer to analyze sales and lead generation performance from a different perspective and establish the appropriate KPIs.
Building a PDF Editor with Low-Code
Our client, a leading digital credential IT startup, needed a lot of internal processes to be optimized. But the experience with low-code tools wasn’t sufficient. That’s why the company decided to hire professionals. And our team of developers joined the project.
The scope of work
The client has a program that designs and prints custom badges for customers. The badges need to be “mail-merged” with a person’s info and turned into a PDF to print. But what is the best way to do it?
Our developers decided to use Retool as a core tool. Using custom components and JavaScript, we developed a program that reduced employees' time for designing, putting the data, verifying, and printing PDF badges in one application.
As a result, the new approach significantly reduces the time required by the internal team to organize all the necessary staff for the conference, including badge creation.