In simple terms, digital manufacturing is the process of leveraging digital technologies to benefit operations at an industrial enterprise. The concept helps organizations of all sizes optimize the entire manufacturing process and services with data-driven computer systems.
The Difference and Key Features
Speaking of technology, it’s worth saying that digital manufacturing differs from automated production consisting of siloes connected by integrators. The main difference lies in seamless integration and standardized data formats throughout a product’s entire life cycle.
Another important difference is the speed and convenience of work. Smart enterprises use flexible tooling solutions that are highly adaptable to meet various business needs. While all workers have tablets or smartphones connected to a unified information system, they can easily interact and manage internal processes. For instance, they can receive shift-daily tasks, see reports on their implementation, or communicate with other departments.
Let’s observe the key features of digital manufacturing, shall we?
- Manufacturing processes such as assembly, machining, casting, stamping, etc., are digitally simulated;
- Design errors are detected before goods go into production;
- Quality is improved due to data transparency and real-time exchange between all participants in production chains.
When talking about the biggest benefits of Industry 4.0, industry professionals indicate reduced time and costs associated with developing new products, lean manufacturing, less waste, and moderate energy consumption. What’s more, digitalization allows manufacturers to diversify their offerings with custom products available in small batches.
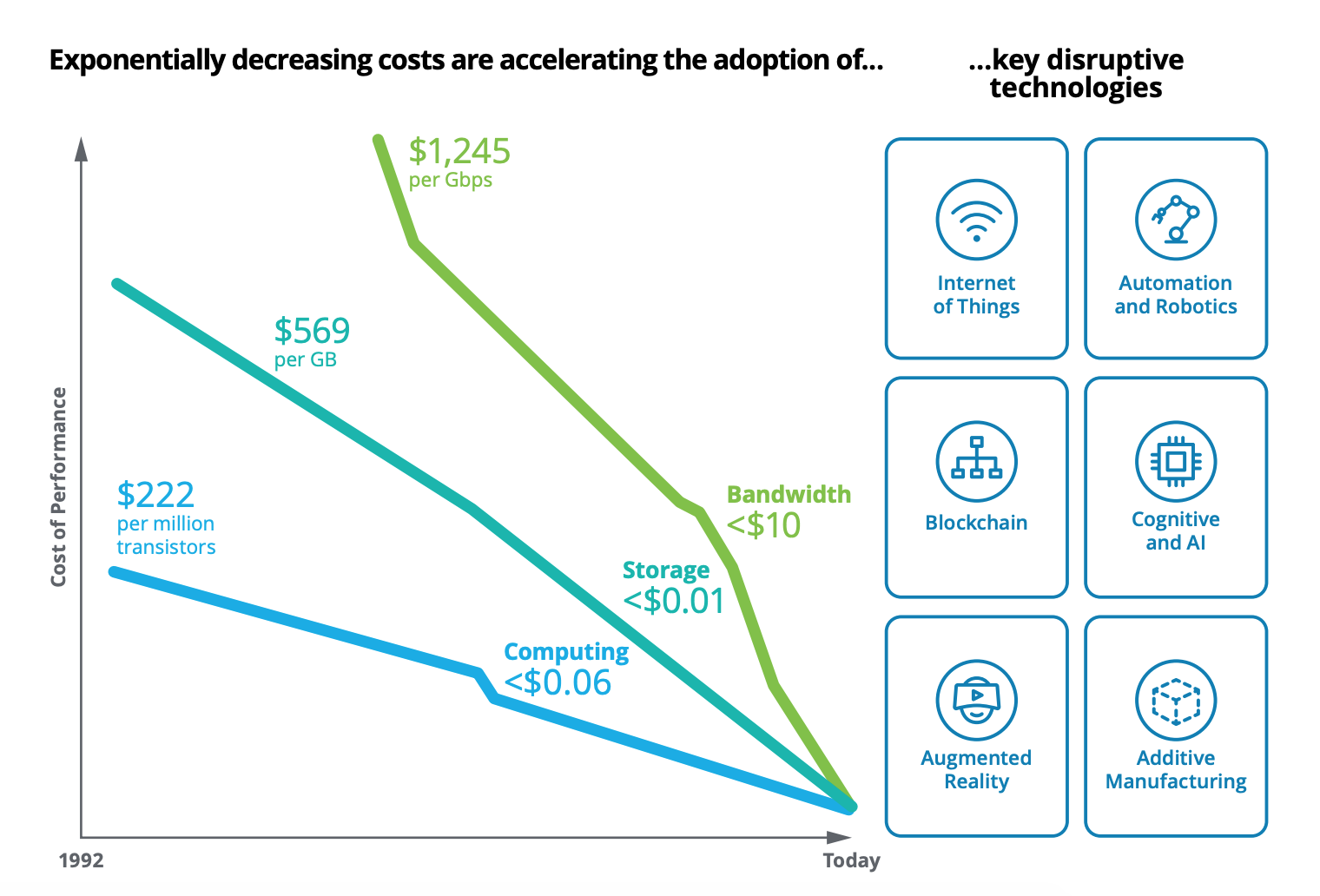
Current Challenges
Nowadays, digital manufacturing and corresponding ecosystems are still at their formative stage in many countries worldwide. The most common issues on the path towards definitive adoption include insufficient project financing, outdated infrastructure, and the lack of qualified specialists. The latter point is especially painful as the sector suffers from a shortage of IT experts with industrial expertise.
Another issue is that high-level executives can’t fully grasp the idea that the digital transition won’t happen overnight. Instead, the process of digitization requires a complex set of measures, time, and patience. More often than not, decision-makers neglect prototyping, modeling, and testing managerial hypotheses before making investments.
The thing is, when a company wastes time creating concepts and reports, instead of prototyping products and modeling business processes, one can’t expect good results. With that being said, let’s observe the most important pillars of digital manufacturing.
Machine Data Collection
Industry 4.0 is all about creating a single information space so that all automated enterprise management systems and industrial equipment can quickly exchange information. This way, the key step towards the digital transformation of manufacturing is machine data collection. The use of MDC (Machine Data Collection) and MDA (Machine Data Acquisition) systems allows operators to collect data on production facilities (equipment, employee workplaces, service departments, etc.) for production management purposes.
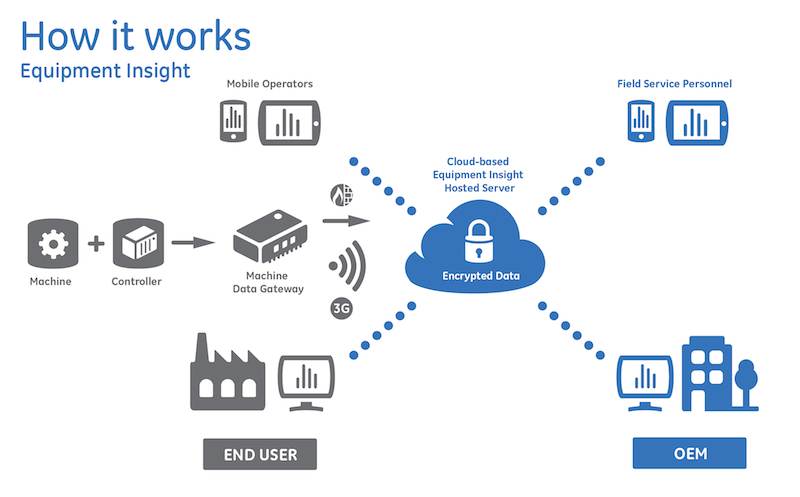
Speaking of increasing production efficiency, manufacturers place big bets on the Industrial Internet of Things, or IIoT. Industry analytics expect that IIoT will help digitize the entire product chain, create intelligent manufacturing and significantly increase its efficiency.
The Industry 4.0 concept doesn’t imply that machines should operate without humans. Instead, it’s about people and machines interacting as a single organism. In this regard, MDC/MDA class systems allow improving modern production without significant investments, increase its efficiency and simultaneously solve many related problems.
With machine data collection solutions, manufacturers have a reliable way of capturing and transforming their production data. They can also make precise data-based decisions, drive automation on their factory floors, and dominate the market with an unprecedented competitive advantage.
Digital Twin
A digital twin is a physical device's software analog that simulates a real object's internal processes, technical characteristics, and behavior under various conditions. Digital twin technology allows creating digital copies of market-ready objects and factory prototypes.
This technology is a real game-changer for the industry. As Chris O’Connor from IBM put it: “It's more than a blueprint, it's more than a schematic. It's a virtual representation of both the elements and the dynamics of how an Internet of Things device responds throughout its lifecycle. It can be a jet engine, a building, process on a factory floor, and much, much more”. Before launching a new production line or product, you can digitally prototype its work, calculate possible risks, and adjust the manufacturing process if necessary. For example, in the automotive industry, this technology significantly reduces the time of each stage of design and production.
The creation of digital twins is integral to introducing modern PLM technology (Product Lifecycle Management). In turn, both IIoT and PLM are crucial attributes of a smart factory. The technology's characteristic feature is forming and using a digital model of material flows. In other words, the technology is no longer a separate product but a production system. While the traditional industry largely depends on numerous full-scale, time-consuming, and costly tests, modern enterprises conduct tests using a digital twin and save both time and resources.
The digital twin of the product includes:
- Geometric and structural model of the object;
- A set of calculated data for parts, assemblies, and the product as a whole;
- Mathematical models that describe all physical processes occurring in the product;
- Information about the technological processes of manufacturing and assembly of individual elements and the product as a whole;
- Product lifecycle management system.
Cloud
As of today, it’s evident that the next five years will see widespread cloud expansion and further adoption by enterprises of all sizes. After all, artificial intelligence (and the use of AI systems will simplify the analysis of data stored in the cloud), 3D printing, sensor technology, and other technologies used at a smart factory correlate with the cloud. Therefore, cloud adoption is integral when speaking about the digital transformation of manufacturing businesses.
While it’s true that the migration process is expensive in itself, the report by Synergy Research Group claims that cloud spendings are up. These numbers are logical. Sure enough, you have to spend a little fortune, but the transition to the cloud helps industrial manufacturers economize without bid-budget investments in IT infrastructure, software, licenses, and high-paid employees.
Fair enough, cloud migration challenges exist. Again, the biggest challenge is the lack of proper infrastructure. According to a report by Oracle, as much as 60% of businesses don’t have the proper environment to start innovating. However, the transition to the cloud shouldn’t be seen as a tribute to fancy trends. Instead, it is a market necessity for any organization that embarks on the path towards Industry 4.0.
Cloud is omnipresent. For example, I mean big data processing solutions, model-oriented approaches, widespread use of cyber-physical systems that independently transmit information to the Internet of Things, and cyber security systems.
Final Words
Digital manufacturing describes an industrial enterprise driven by processes that are centered around the use of digital solutions at every stage of the production chain. However, let’s face it: going fully digital requires money, effort, and, most importantly, expertise. No wonder that most enterprises resort to digital transformation consulting services to implement their strategy successfully.
First of all, manufacturers need to realize the need for change and evaluate their digital maturity in collaboration with experts. Industrial companies must follow the global digitalization trend: nowadays, fast and flexible companies are right behind large competitors burdened by regulations and rules. Here at Akveo, we invite you to transform your business processes and reimagine production with Industry 4.0 technologies and Industrial Internet of Things (IIoT) consulting and development services. Contact us today to learn how we can bring connectivity to your enterprise and fulfill your clients’ requests faster.
Streamlining Gifting Marketplace Operations with Retool
Afloat, a gifting marketplace, needed custom dashboards to streamline order management, delivery tracking, and reporting while integrating with Shopify and external APIs.
The solution:
We built two Retool-based dashboards:
- A Retail Partner Dashboard embedded into Shopify for managing orders and store performance.
- An Admin Dashboard for handling deliveries and partner data.
Both dashboards included real-time integration with Afloat's Backend and APIs for accurate, up-to-date data and scalability.
The result: enhanced efficiency, error-free real-time data, and scalable dashboards for high-order volumes.
Billing Automation for a SaaS Company with Low-Code
Our client needed a robust billing solution to manage hierarchical licenses, ensure compliance, and automate invoicing for streamlined operations.
The solution:
We developed a Retool-based application that supports multi-tiered licenses, automates invoicing workflows, and integrates seamlessly with CRM and accounting platforms to enhance financial data management.
The result:
- Achieved 100% adherence to licensing agreements, mitigating penalties.
- Automated invoicing and workflows reduced manual effort significantly.
- Dashboards and reports improved decision-making and operational visibility.
Retool Dashboards with HubSpot Integration
Our client needed a centralized tool to aggregate account and contact activity, improving visibility and decision-making for the sales team.
The solution
We built a Retool application integrated with HubSpot, QuickMail, and Clay.com. The app features dashboards for sorting, filtering, and detailed views of companies, contacts, and deals, along with real-time notifications and bidirectional data syncing.
The result
- MVP in 50 hours: Delivered a functional application in just 50 hours.
- Smarter decisions: Enabled data-driven insights for strategic planning.
- Streamlined operations: Reduced manual tasks with automation and real-time updates.
Lead Generation Tool to Reduce Manual Work
Our client, Afore Capital, a venture capital firm focused on pre-seed investments, aimed to automate their lead generation processes but struggled with existing out-of-the-box solutions. To tackle this challenge, they sought assistance from our team of Akveo Retool experts.
The scope of work
The client needed a tailored solution to log and track inbound deals effectively. They required an application that could facilitate the addition, viewing, and editing of company and founder information, ensuring data integrity and preventing duplicates. Additionally, Afore Capital aimed to integrate external tools like PhantomBuster and LinkedIn to streamline data collection.
The result
By developing a custom Retool application, we streamlined the lead generation process, significantly reducing manual data entry. The application enabled employees to manage inbound deals efficiently while automated workflows for email parsing, notifications, and dynamic reporting enhanced operational efficiency. This allowed Afore Capital's team to focus more on building relationships with potential founders rather than on administrative tasks.
Retool CMS Application for EdTech Startup
Our client, CutTime, a leading fine arts education management platform, needed a scalable CMS application to improve vendor product management and user experience.
The scope of work
We developed a Retool application that allows vendors to easily upload and manage product listings, handle inventory, and set shipping options. The challenge was to integrate the app with the client’s system, enabling smooth authentication and product management for program directors.
The result
Our solution streamlined product management, reducing manual work for vendors, and significantly improving operational efficiency.
Building Reconciliation Tool for e-commerce company
Our client was in need of streamlining and simplifying its monthly accounting reconciliation process – preferably automatically. But with a lack of time and low budget for a custom build, development of a comprehensive software wasn’t in the picture. After going through the case and customer’s needs, we decided to implement Retool. And that was the right choice.
The scope of work
Our team developed a custom reconciliation tool designed specifically for the needs of high-volume transaction environments. It automated the processes and provided a comprehensive dashboard for monitoring discrepancies and anomalies in real-time.
The implementation of Retool significantly reduced manual effort, as well as fostered a more efficient and time-saving reconciliation process.
Creating Retool Mobile App for a Wine Seller
A leading spirits and wine seller in Europe required the development of an internal mobile app for private client managers and administrators. The project was supposed to be done in 1,5 months. Considering urgency and the scope of work, our developers decided to use Retool for swift and effective development.
The scope of work
Our developers built a mobile application tailored to the needs of the company's sales force: with a comprehensive overview of client interactions, facilitated order processing, and enabled access to sales history and performance metrics. It was user-friendly, with real-time updates, seamlessly integrated with existing customer databases.
The result? Increase in productivity of the sales team and improved decision-making process. But most importantly, positive feedback from the customers themselves.
Developing PoC with Low Code for a Tour Operator
To efficiently gather, centralize, and manage data is a challenge for any tour operator. Our client was not an exception. The company was seeking to get an internal software that will source information from third-party APIs and automate the travel itinerary creation process. Preferably, cost- and user-friendly tool.
The scope of work
Our experts ensured the client that all the requirements could be covered by Retool. And just in 40 hours a new software was launched. The tool had a flexible and easy-to-use interface with user authentication and an access management system panel – all the company needed. At the end, Retool was considered the main tool to replace the existing system.
Testing New Generation of Lead Management Tool with Retool
Our client, a venture fund, had challenges with managing lead generation and client acquisition. As the company grew, it aimed to attract more clients and scale faster, as well as automate the processes to save time, improve efficiency and minimize human error. The idea was to craft an internal lead generation tool that will cover all the needs. We’ve agreed that Retool will be a perfect tool for this.
The scope of work
The project initially began as a proof of concept, but soon enough, with each new feature delivered, the company experienced increased engagement and value.
We developed a web tool that integrates seamlessly with Phantombuster for data extraction and LinkedIn for social outreach. Now, the company has a platform that elevates the efficiency of their lead generation activities and provides deep insights into potential client bases.
Building an Advanced Admin Portal for Streamlined Operations
Confronted with the need for more sophisticated internal tools, an owner of IP Licensing marketplace turned to Retool to utilize its administrative functions. The primary goal was to construct an advanced admin portal that could support complex, multi-layered processes efficiently.
The scope of work
Our client needed help with updating filters and tables for its internal platform. In just 30 hours we've been able to update and create about 6 pages. Following features were introduced: add complex filtering and search, delete records, styling application with custom CSS.
Together, we have increased performance on most heavy pages and fixed circular dependency issues.
Creating MVP Dashboard for Google Cloud Users
Facing the challenge of unoptimized cloud resource management, a technology firm working with Google Cloud users was looking for a solution to make its operations more efficient. The main idea of the project was to create an MVP for e-commerce shops to test some client hypotheses. Traditional cloud management tools fell short.
The scope of work
Determined to break through limitations, our team of developers turned Retool. We decided to craft an MVP Dashboard specifically for Google Cloud users. This wasn't just about bringing data into view; but about reshaping how teams interact with their cloud environment.
We designed a dashboard that turned complex cloud data into a clear, strategic asset thanks to comprehensive analytics, tailored metrics, and an intuitive interface, that Retool provides. As the results, an increase in operational efficiency, significant improvement in cost management and resource optimization.
Elevating CRM with Custom HubSpot Sales Dashboard
Our other client, a SaaS startup, that offers collaborative tools for design and engineering teams, was on a quest to supercharge their sales efforts. Traditional CRM systems were limited and not customizable enough. The company sought a solution that could tailor HubSpot to their workflow and analytics needs.
The scope of work
Charged with the task of going beyond standard CRM functions, our team turned to Retool. We wanted to redefine how sales teams interact with their CRM.
By integrating advanced analytics, custom metrics, and a user-friendly interface, our developers provided a solution that transformed data into a strategic asset.
In 40 hours, three informative dashboards were developed, containing the most sensitive data related to sales activities. These dashboards enable our customer to analyze sales and lead generation performance from a different perspective and establish the appropriate KPIs.
Building a PDF Editor with Low-Code
Our client, a leading digital credential IT startup, needed a lot of internal processes to be optimized. But the experience with low-code tools wasn’t sufficient. That’s why the company decided to hire professionals. And our team of developers joined the project.
The scope of work
The client has a program that designs and prints custom badges for customers. The badges need to be “mail-merged” with a person’s info and turned into a PDF to print. But what is the best way to do it?
Our developers decided to use Retool as a core tool. Using custom components and JavaScript, we developed a program that reduced employees' time for designing, putting the data, verifying, and printing PDF badges in one application.
As a result, the new approach significantly reduces the time required by the internal team to organize all the necessary staff for the conference, including badge creation.